This article relates to the Rotax brand, although there are others in use, their numbers are small and I don�t have first hand experience with them.
As you probably know, two strokes have a bad rep. Most of it is well deserved and they do quit, however there is more to that story and it really doesn�t have to be that way.
Here are the reasons, first the generic, the two stroke engines require to be installed and operated (tuned) in a specific way which is different then your average GA four stroke, the difference is actually small but the consequence of not following the rules is far les forgiving with severe bad results .
Unfortunately, the manufacturer itself makes no attempt to educate the user how to run these engines properly, in the enclosed manual they tell you the max RPM,EGT, CHT range and that�s it, there is absolutely no mentioning how to select the correct prop for the speed range of the aircraft and how strongly the load on the engine affects its tuning (Rich/Lean) which happens to be one of the most common reasons for the engine seizures.
Now, that the word seizure is out , we have to know what it is and what causes it. Two main reasons cause the seizure.
1- high temperature difference between the cylinder and the piston which will result in insufficient clearance between the two and causing too high friction , melting the side of the piston and smudging it onto the cylinder wall,
2 - lack of lubrication, creating basically the same result .
What prevents the seizure under normal running condition,
1- we mix oil with gasoline or sometimes inject it (better way when done properly), to keep those parts lubricated.
2- keep the temperatures - specially that of the piston under control and this is the tricky part, the piston is cooled by the fresh cool air/fuel mixture entering the crankcase and by keeping the combustion (EGT) low enough by setting the mixture on richer - cooler burning side. Here you can see how leaning the mixture is a double edge sword , the combustion temperature (EGT) goes up and at the same time amount of oil for lubrication is reduced. This is why a seizure is most likely caused by the combination of the two factors rather then one or the other.
Here is the most important fact, the two strokes, not having the valves to control the fuel charge/exhaust discharge rely on so called tuning of the engine, which is a function of the exhaust system , piston porting, carburetor setting, and (Which is almost newer mentioned but equally important ) - the load on the engine, all these factors must be in harmony, and you can�t for example make up for too low engine load (which creates lean condition - high EGT) by increasing the jet sizes to make up for it and lower the EGT that way. Why you ask, because now your carburetor is out of tune from the "piston porting " and exhaust system design, two wrongs will not make one right, you may manage to keep the engine from seizing that way , but fuel consumption will be high, temperatures will read odd , peak power will be less and carbon will build up faster.
So now (if you�re still reading this) if so many of these seizures are caused by too low engine load why does it happen so often. Here are the typical reasons.
1. The pilot is descending in a shallow descent at a relatively high airspeed and throttle partially open (about half way or so). This is very dangerous setting, the mixture will lean out significantly but it does not necessarily shows up as too high EGT because the engine is not really producing much power and remember its not necessarily over the limit EGT but rather the difference between the piston and cylinder temperature . All three bad conditions are met here , combustion (piston) temperature is high, cylinder temperature is low (not much power produced) and low amount of oil entering the engine. Even an engine that is otherwise well tuned can seize this way.
I recommend to do your descending at only slightly above or at idle rpm at slow airspeed somewhere between best glide and best sink.
2. Static rpm too high caused by pitch on the prop set too low. Many people seem to think that if the book for their 503 engine states max hp develops at 6500 , that�s what they should set it for (down on the ground), some even believe the more rpm, the more power they get and use the max rpm number .These numbers are way too high are very likely to cause very lean mixture conditions in flight, because when the aircraft is in motion the prop unloads and the rpm will soar , then in cruise mode with the throttle retarded to keep the rpm in check very lean running condition is created, this should be indicated by high EGT but often people don�t pay enough attention to these warning signs , and/or don�t realize how dangerous this really is until its too late.
The static rpm should be set well below the max hp rpm and the optimum depends largely on the speed range of the aircraft, generally the higher the cruise/top speed the lower the static rpm is set even if that means lower then max hp rpm in climb mode. Only on very high drag aircraft with very narrow speed range you can set the static rpm higher so it gets close to max hp in the climb mode as you will not unload the engine on such an aircraft even when you level off to cruise.
3. Another potentially bad combination is using very large (diameter / blade area) prop for a given engine, in which case the pitch must lowered considerable to bring the engine up to the acceptable RPM. In this case, even when the static rpm is rather low, the engine load will start dropping very rapidly as soon as the aircraft start gaining the speed . Only very slow aircraft can use such a combination successfully , perhaps a special purpose one like a hang glider tow plane or a powered parachute.
Unfortunately I see just such bad a combination on the new Ison�s airplane. They are using 62 inch powerfin prop, 2.5 gear ratio, on only 22 hp (???) , that�s a very large prop for that engine, In my guess the pitch will have to be no more then about 23-24 inches . If I�m correct, with this combination at 6000 rpm the prop blades will be at zero angle of attack and zero thrust as soon as the airplane reaches airspeed of about 55 mph.
4. During past 15 or so years with the ultralight movement on the rise, many conventional aircraft designers, some of them well known and capable, realized the great potential of these small size, light weight , low power two strokes have to be used for a new kind of very small, light and fast aircraft, I mean low power by their standards as anything under 100 hp is low power to them, a number of them were build but unfortunately quickly found out about the pitfalls of those little two strokes and usually the hard way. Many experienced engine failures early in flight testing , many aircraft were destroyed , the little two strokes were labeled unreliable and unsuitable for "real" airplanes and projects abandoned, creating a good part of the bad reputation. It is my believe that this low success was mainly for the lack of knowledge of how to use these engines properly, they had no experience with them and tried to use them in a very difficult application, not knowing the difference from the old four strokes .
There is however at least one great success story . The Mike Arnold�s AR-5 powered by rotax 582 holds the word speed record in the up to 660 lb category - 212 mph (or something like that). To hear from Mike himself click here
Another very good page written on the same subject in different words is here
Legal disclaimer: This article is only a one man�s opinion and may contradict with experience and advice of others .
 |
Rotax 447 undergoing 150 hours inspection. The main task is decarboning , especially the ring groves , this is the second time we are inspecting this engine, and each time the bottom rings were found partially stuck in the grove. We are also changing the crank seals so the case is split and the flywheel and the front gear is pulled from the crankshaft.
|
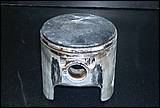 |
This is what a seized piston looks like. This one belongs to Spark from Flightstar, not a lot of damage but resulted in in a forced landing in his 503 powered float equipped Loadstar . The reason was probably a combination of installing the aftermarket tuned pipe for more power, too lean mixture and to low prop pitch .
|
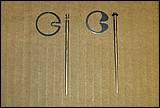 |
Many people (me included) had problems in the past with the carburetors when the jet needle got worn in the clip grove by the badly designed needle clip which allowed vibrating and spinning of the needle . This is greatly improved by the new clip design but still needs to be checked regularly for wear.
On the left is the old clip and the jet needle with all the groves completely worn out, it didn�t take long for it to happen and I landed on the radio control field in the middle of the contest because of this.
On the right is the new clip design plus note the little O-ring on the needle.
|
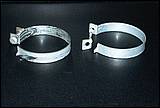 |
Another possible problem that may sneak up on you is breaking of the clamp holding the carburetor boot . This is very hard to see its about to happen even when checking regularly. I have two in my collection one from my friends 277 powered Mitchell wing and one broke on me recently. It�s a good idea to have some secondary provision which will hold the carburetor in place and prevent it from falling off should the clamp break.
|
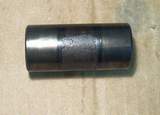 |
Worn out wrist pin. The hard coating is gone about a third around. This is why you need to do the 50 hours inspections and why you need to remove the cylinder and the piston so you can inspect everything and not just take off the cylinder heads , scrape the carbon from the top of the piston and call it done. This one was caught just in time but a little longer and the needle bearing would disintegrate ruining the connecting rod and requiring new crankshaft assembly.
|
Back to main page